Unfortunately we had to go get a new builder, so we have been pushed back by six months to the end of his queue and the cost of the build has jumped by over €100k. Which really sucks.
What went wrong?
The builder we had up until now had started making cold feet noises around October of last year. Up until then he was taking us to Builder’s Finish, now he was refusing to give quotes for Builder’s Finish and would only talk about Timber Frame Supply and Install, which isn’t what I had wanted as I had been specifically seeking project management. That got worse as we approached Christmas, and despite me having paid him a retainer, getting information about what he was willing to build and for what price became ever harder. As we are not building a standard Irish house, but rather the first certified Passive House Plus (note the Plus, it is one grade stricter than normal Passive House), we can’t and never were going to be able to use standard Irish build techniques. Indeed, we can’t even use standard Passive House techniques. The builder who has many years of experience building Passive House, knew we were targeting certified Plus from the outset. But I don’t think he was prepared for just how custom that was going to make the build, and time needed to define cost effective build approaches in the very shallow Irish building supplies market where there isn’t much choice, and prices for some materials are unusually high compared to elsewhere in Europe. As we didn’t know and couldn’t know if some material combination was cost effective or whether the builder was willing to do it at all, that necessarily involved a lot of back and forth, and the builder he was not supportive of this dialogue.
Furthermore, as recounted last entry, over Christmas we had to move from rigid phenolic foam insulation to 300 mm cellulose which needed a twin stud, as the unusually humid Banteer climate is too much for rigid foam insulation. That obviously needs more work to make the frames, and more insulation to fill them. So just as we were about to pay the first big deposit, in came a revised quote €110k higher. This came as bit of a shock at the time. It was 31% higher than the preceding quote.
Now, to be fair, I think that quote was fair for the spec involved. I didn’t think so at the time obviously, so I went and re-sought quotes for the post-Christmas build spec, some came in under, some over, but the ballpark was similar. To put it bluntly, if you move from a 0.16 u-value to a 0.11 u-value, that is a 31% improvement in insulation. The considerably thicker walls now need more timber, more support, more effort to manufacture to nail all those bits of timber together. It is as simple as that: one third more house costs one third more.
Choosing a new builder
While our former builder had given a fair quote I think, unfortunately once you enter that price per sqm now being charged, the landscape changes somewhat. At sub-€1,000 per sqm for sub and super structure supply and install, you get an economy-orientated custom design house build, so while the design is unique (and therefore a step above a catalogue once off build), there will be a single cost-optimised system and you can’t deviate from it (as has since become very obvious). In addition to a fixed choice build system, there will be various small compromises in terms of customer experience and build quality, but overall you get good bang for your buck, if you’re happy with what that system delivers.
However once you’re into the ~€1,250 per sqm shell price range, you’re getting into wealthy person builder territory – as in, the kind of builder who caters only to the very wealthy, where custom build-ups, custom materials, and custom ways of assembling them become more normal. This is because you’re now into performance-orientated or quality-orientated building, rather than optimising mostly for cost.
As an example, take Advanced Housing Systems who are a British based builder we got a quote from. They take you to nearly the end of First Fix, with only electricals, plumbing, and ventilation missing – but all the internal plasterboard and insulation is done (you might wonder how this works, they build conduit and ducting into their premanufactured panels for all the wiring, plumbing etc). They only use wood cut from their own forest in Devon, and only sheep’s wool from their own flock of sheep as insulation. Everything is done in-house, no subcontractors, so everything gets the personal touch. They’ll deliver and install your house anywhere in greater Europe, from an empty site they are done within one month.
This probably sounds expensive, but they come in at €2,083 inc VAT per sqm. That price includes M&E design, structural design, all the engineering, getting the stuff over to Ireland and hotels for the workers to erect it. Once everything is factored in, they’re actually very price competitive overall to an Irish builder, all the u-values are 0.10 compared to the 0.15’s you see from ‘passive standard’ builders, theirs is undoubtedly a superior quality build for the discerning client. And you’re probably thinking there must be a catch here?
Indeed there is: it’s financing. There are three mortgage lenders in Ireland who do self builds. Their stage payments are hardcoded to six stages based on the assumption everybody builds a concrete block house, and they pay in arrears. They do not allow for the large advance payments necessary to fund the offsite construction of timber frames. They do not allow borrowing in addition to the mortgage. You therefore need to front huge amounts of unborrowed cash in advance, and for that, you need to have in your bank large amounts of cash. Which I do not, as I’ve spent it as you’ve seen in the quarterly House build spend updates.
AHS because they supply more than most in their package they have larger upfront cash flow needs than most, so how Irish bank mortgages work is particularly ill suited for them especially, and that was the sole reason I had to rule them out (I would have loved to have chosen them otherwise). And, in fact, this same problem of financing also affected the former builder, because he supplied all the plasterboard and internal insulation (unfitted) you’ll need, and thus like with AHS his higher cost quote created a substantial cash flow problem for me. When he increased his quote by that much, it’s not that I couldn’t afford it overall, it’s that I can’t raise the cash flow to make the stage payments paid in arrears work anymore. You may remember that my mortgage is capped to 90% of valuation, so I can’t borrow more, I can’t borrow elsewhere, and I just don’t have the cash needed nor can I get it. It’s as simple as that.
So, when choosing a new builder, I had to choose ‘less is more’: the less they supplied in their package in one go, the less cash upfront I needed before the bank mortgage pays out in arrears. Paradoxically, this almostly certainly increases the overall cost as much more now needs to be done by direct labour, also it also hugely increases the amount of project management I need to do as much more needs to be done now once the builder has departed. Most unfortunate, but that’s the main reason why poor people remain poor: they don’t have the cash flow to avoid being forced into expensive poorly timed purchases. Same principle applies here: my lack of cash flow will increase my costs overall.
The builder chosen: Long Life Structures from Galway
We ended up plumping for Long Life Structures from Galway who have quoted the supply and install of foundations and timber frame for €1,234 inc VAT per sqm to airtightness. Internal partitions will be studded out, but all internal insulation and plasterboard will be supplied by me. It also doesn’t include the considerable fees I have spent and have yet to spend on M&E design and structural engineering, which the AHS quote included. As I mentioned earlier, I think the AHS quote cheaper overall, and certainly for the u-values for the euro they are far better bang for the buck, but in cash flow terms I can’t afford AHS.
LL Structures aren’t too bad for the u-values though in their standard buildup (which is a cost optimised derivative of those from Ecological Building Systems):
- Floor: 0.10
- Wall: 0.134
- Roof (sloped): 0.15
- Roof (flat): 0.09
These u-values are from my own calculations incidentally. You may not be surprised to learn that some u-value claims by some builders don’t add up. LL Structures actually claim worse u-values than the Passive House u-value calculation method, so I think those numbers above are almost certainly an upper bound, and we’ll get quite a bit better than those in practice. More like walls and sloped roof at 0.11.
What isn’t described by u-values alone is thermal bridging, which is something a lot of ‘passive standard’ builders particularly skimp on when thermally breaking the timber studs from bridging between inside and outside (u-values are the average, thermal bridges are the quality). You may see no thermal break at all, or a 25 mm or 50 mm break, and usually to the inside of the AVCL as that is cheaper though inferior, as it moves the interstitial condensation boundary inwards, which means you get things like condensation around the edges of your window frames, which can become mould growth. LL Structures apply 80 mm of thermal break to the wall studs, and it is on the outside not inside which is the more expensive but superior option. Similarly, for their flat roof they thermally break the rafters on the outside with 130 mm of unbroken cellulose. Where they do fall a bit short (as you can probably guess from the u-values above) is on the sloped roof, there the rafters are only mildly thermally broken, using a 220 mm + 75 mm nailed together stud, which is still better than an unbroken stud. The 295 mm space is fully filled with cellulose. We do have roof windows, however if you use the more expensive insulated flashings then moving the interstitial condensation boundary inwards by adding more insulation internally won’t produce the same mould problems as you’d get for wall windows, so that should work okay.
As would be usual for builders in their per sqm price range, they use only 100% natural materials and nothing synthetic, so no PIR board for insulation, no plastics, nothing with volatile organic compounds except where required by law (timber preservative impregnation). Like with AHS, they don’t use subcontractors, everything is done in house by their own employees to ensure the personal touch. Obviously I did ask around about them before hiring them, multiple independent sources said they were good. I pulled all their recent company accounts from the public record, they had a bad few years from covid lockdowns and the build material costs going up so suddenly, but they’re back into profit as of last year. I went to see one of their sites mid-build, construction quality and detail was better than average. I saw multiple small touches here and there, stuff most builders don’t bother doing. Nice.
Here’s hoping it’s all smooth sailing from now on!
New Passive House certifier
Passive House certification comes in two stages: (i) design preassurance and (ii) the actual certification. Bob Ryan our certifier, has decided to retire from certifying so he had only done (i). That means I will need to hire somebody to replace him for (ii), which is inconvenient.
I have received a quote from a potential replacement, and hopefully that will be the end of yet another thing going wrong.
New mortgage
As there is now no way of drawing down the mortgage before May, we will
need it extended. However the cost has also gone up, so of course they
want me to reapply in full from scratch .
Which is something like the third time I’ve had to supply them with all
my financial statements blah blah blah.
I’ve been effectively applying for the mortgage now for two years. I’m going to have to go rejump all those hoops once again like a good little show pony. It’s getting really very tiresome. This is the kind of hassle and inconvenience which results when you change builder last minute – if you can, try to avoid doing so yourself!
Still no entrance door
Last post I had a picture and a cool video for a Sika entrance door. I was hopeful of acquiring one at the time, since I am not.
Sometimes it really sucks to be on an island far off the coast of Europe, and nowhere near a big enough city. Finding decent entrance doors for a good price really shows this. That Sika entrance door (manufactured in Northern Ireland) had a quote for a cool €4,990 inc VAT for supply and install. I know for a fact you can pick up the door in Dublin for under €2k inc VAT, but then you’d need to transport it and install it.
€5k is at least better than the €9k Internorm wanted to supply and install their entrance door. But both quotes are quite frankly ridiculous. It’s a single fucking door, it’s not worth the cost of replacing my or Megan’s car, which is what a spare €5k would do for us. I did hunt around for other reasonably priced doors and we’ve shrunk the door opening to a standard 1000 x 2100 to aid that, however I’m currently thinking I’m just going to ask Nordan for the entrance door too, despite that their entrance doors kinda suck. It’s just easier and there are bigger fish to fry.
New pictures of insides
Last post I mentioned that there had been a few design changes after the PH design assurance stage, mainly that the walls have become thicker and the steel structural support has been moved inside the airtightness layer. Two years ago I rendered images using the then state of the art Unreal Engine 5 which involved a lot of work to convert the BIMX to TwinMotion, and from there to UE5. Back then, the 3D render from Graphisoft for their BIMX was best described as ‘basic’, but they’ve made very significant strides forward even in the past six months such that these look okay, and my urge to render them via UE5 isn’t as strong.
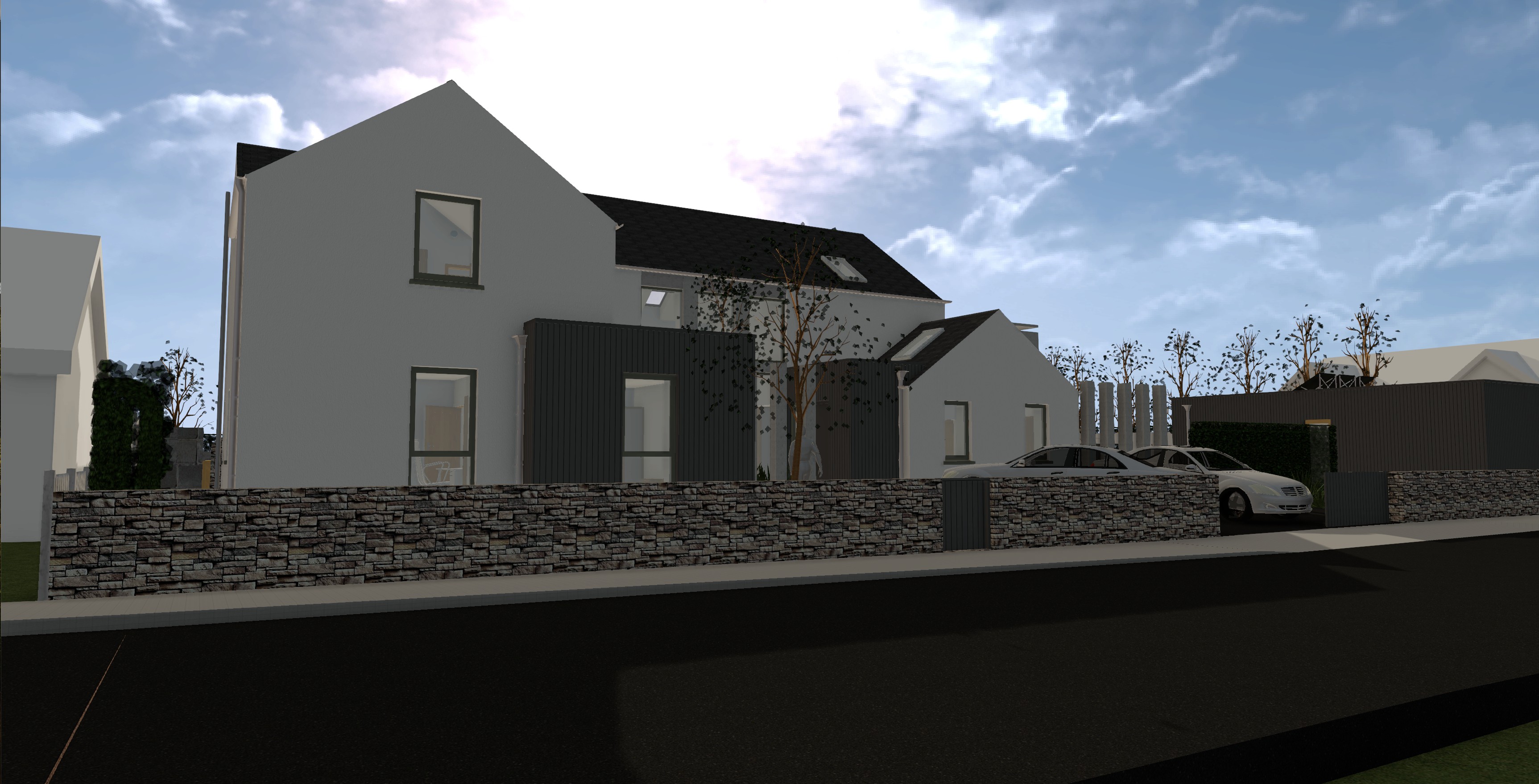
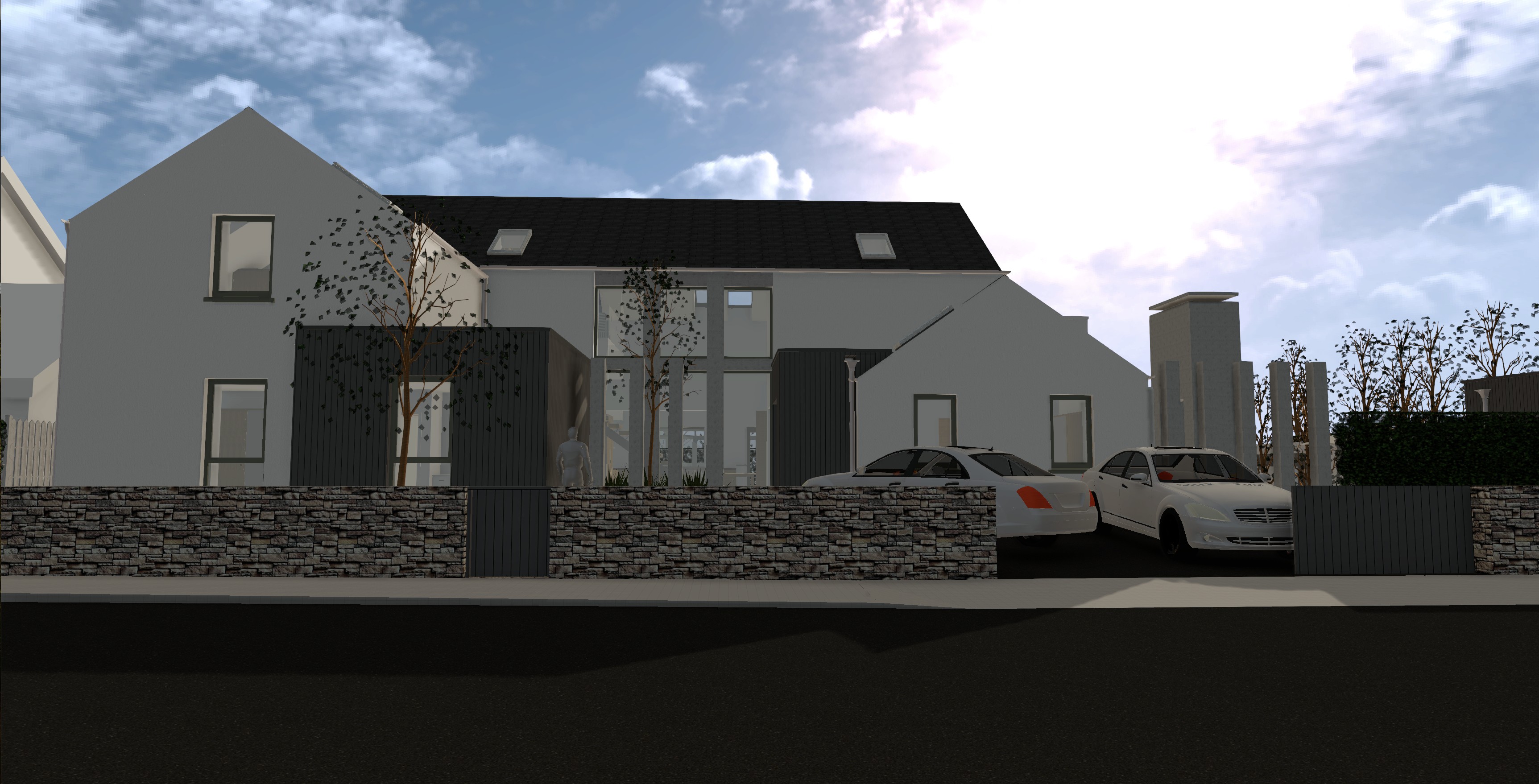
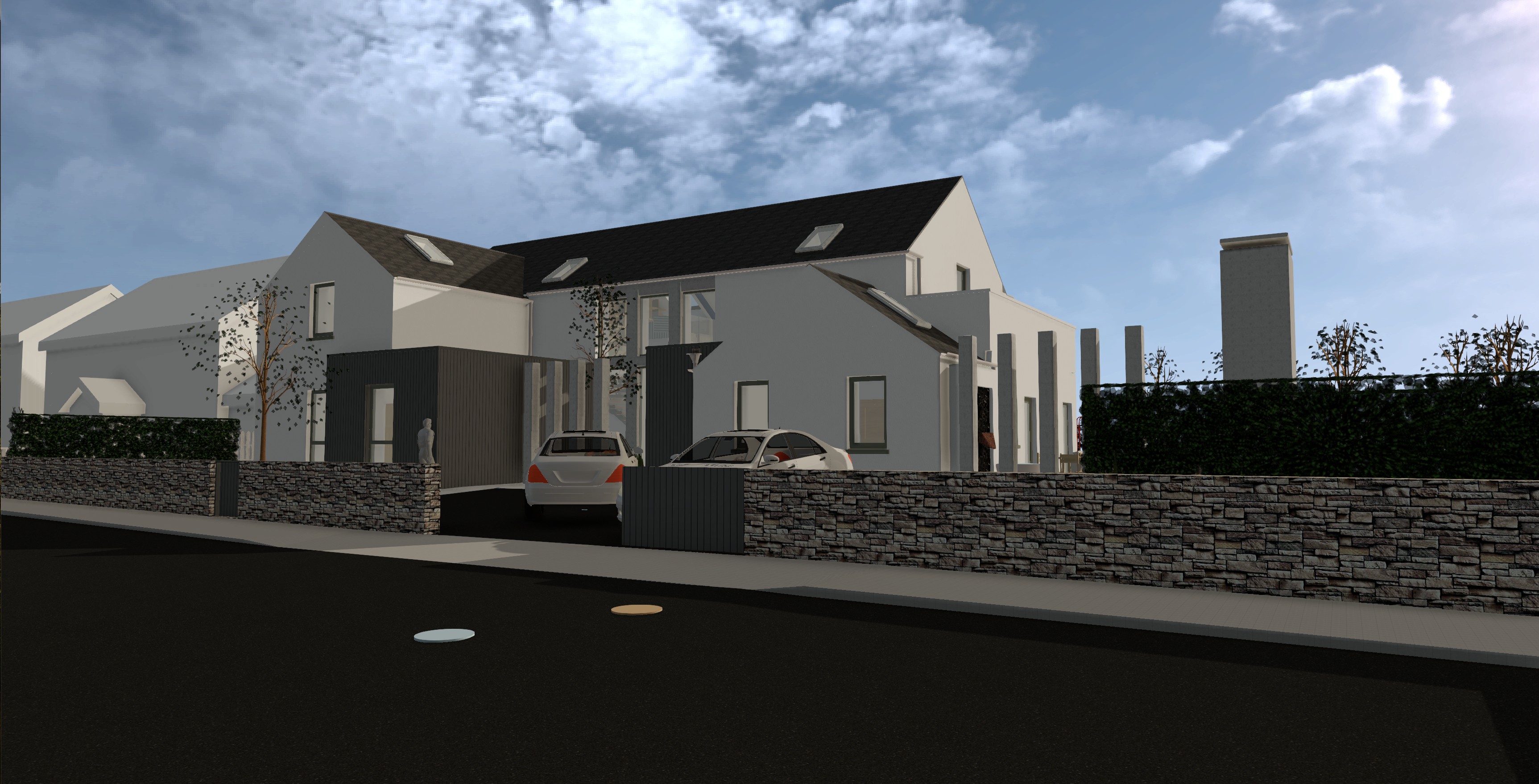
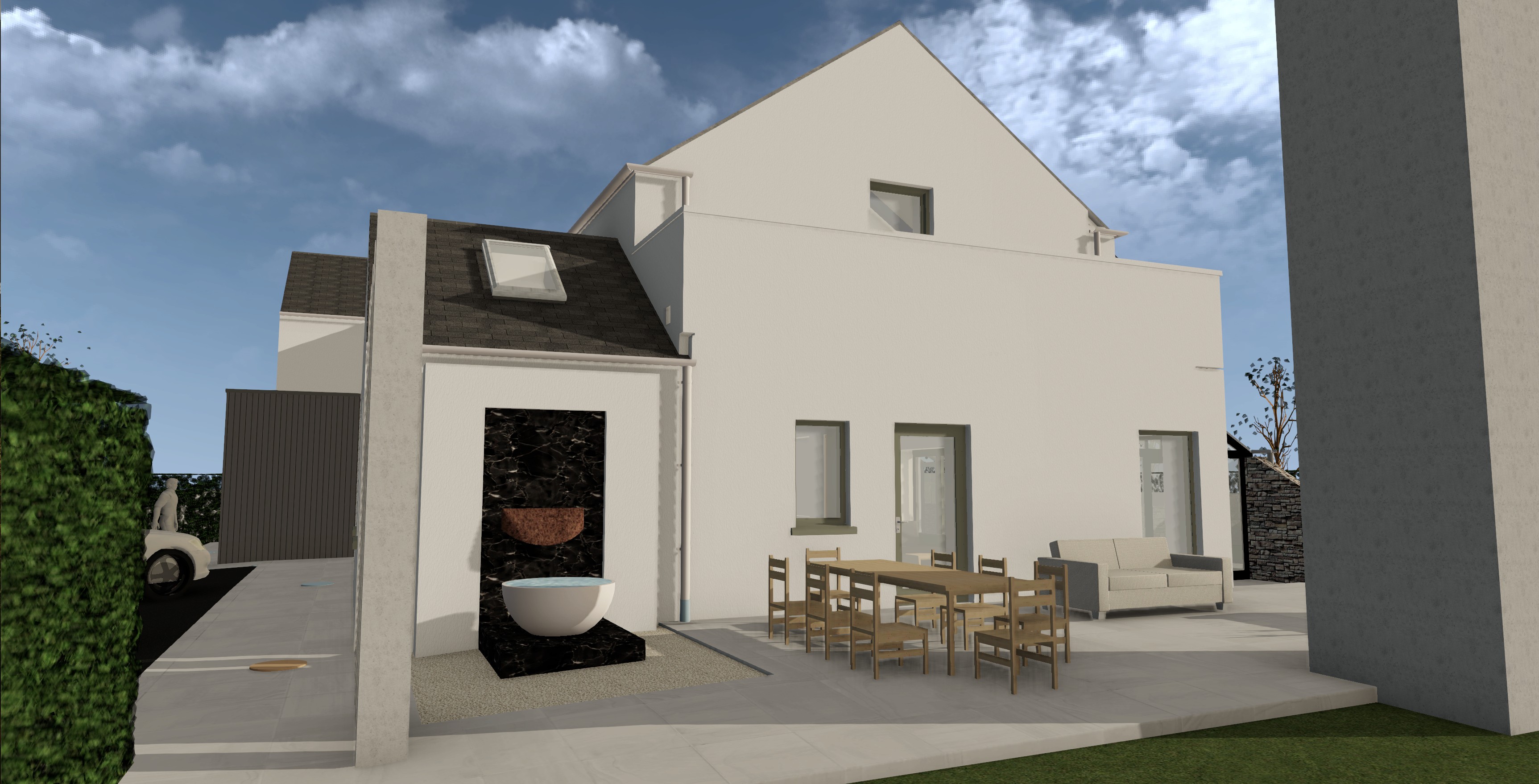
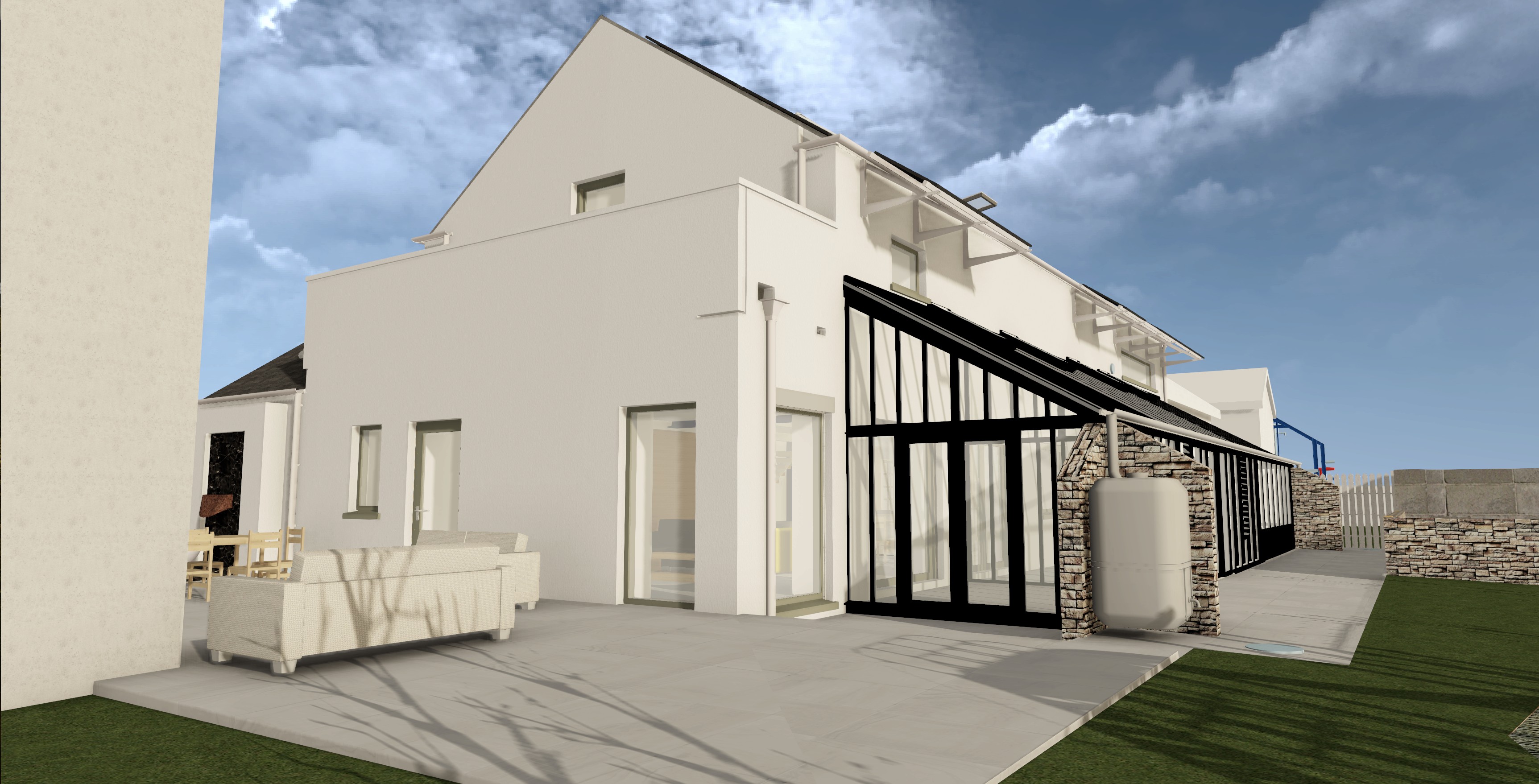

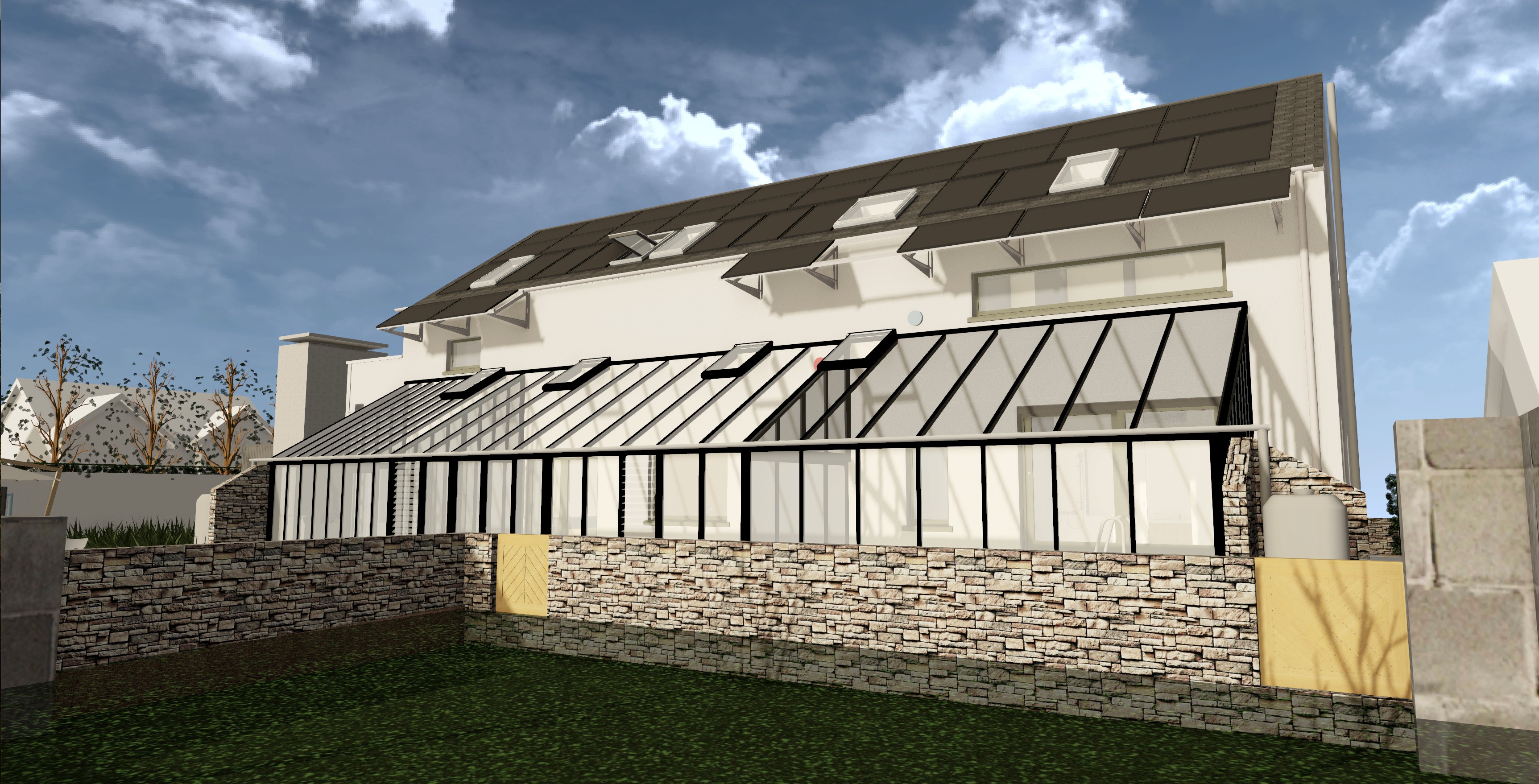
Those definitely aren’t terrible, there is now a reasonable attempt at accurate shadows and lighting, and the high resolution skydome does no harm either. Without doubt nowhere near as good as Unreal Engine 4 never mind 5 – the lack of light bounce and reflection is especially noticeable – but these are sufficiently good that I’m not leaping up and down to go through the hassle of a TwinMotion to UE conversion cycle. These will do.
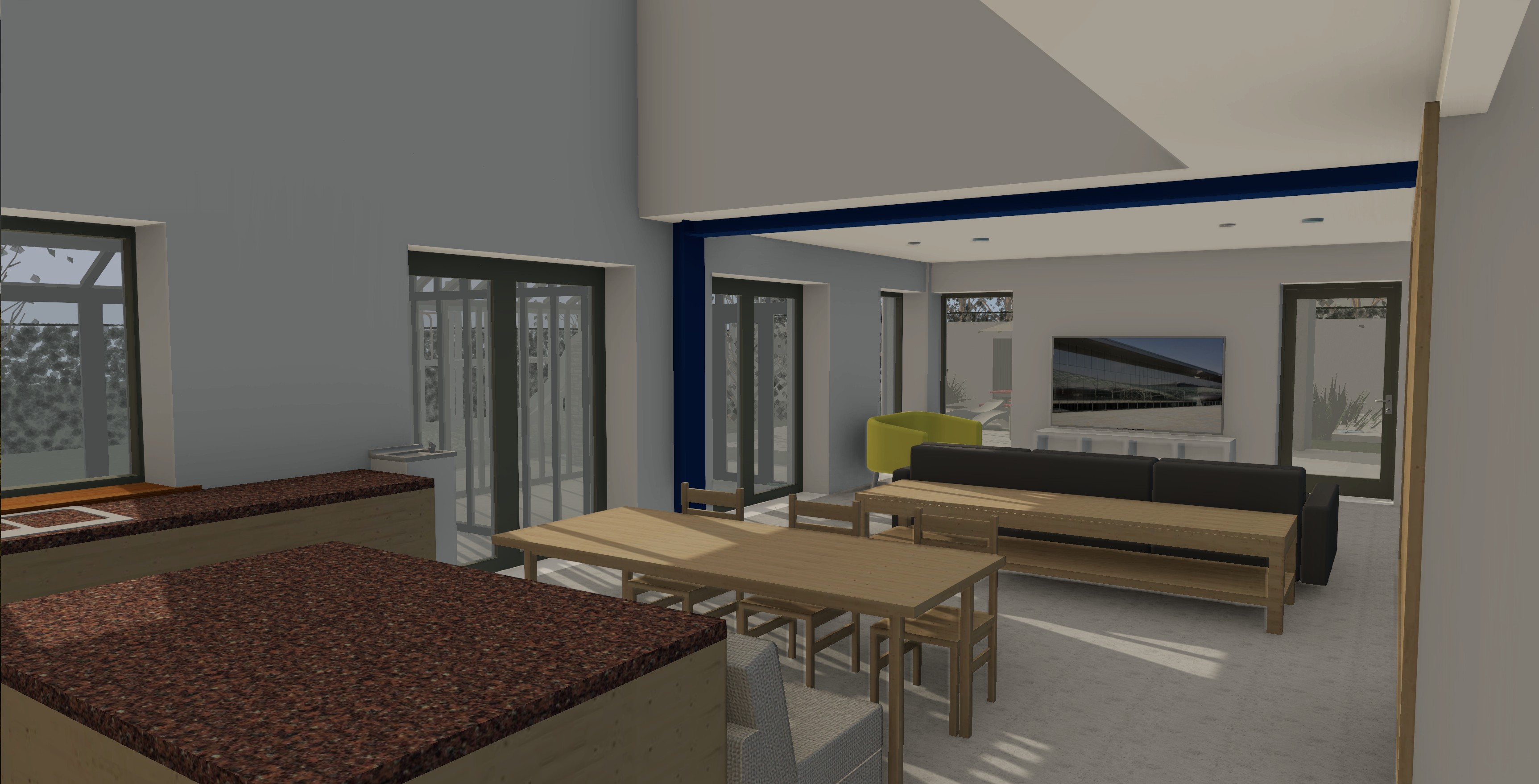
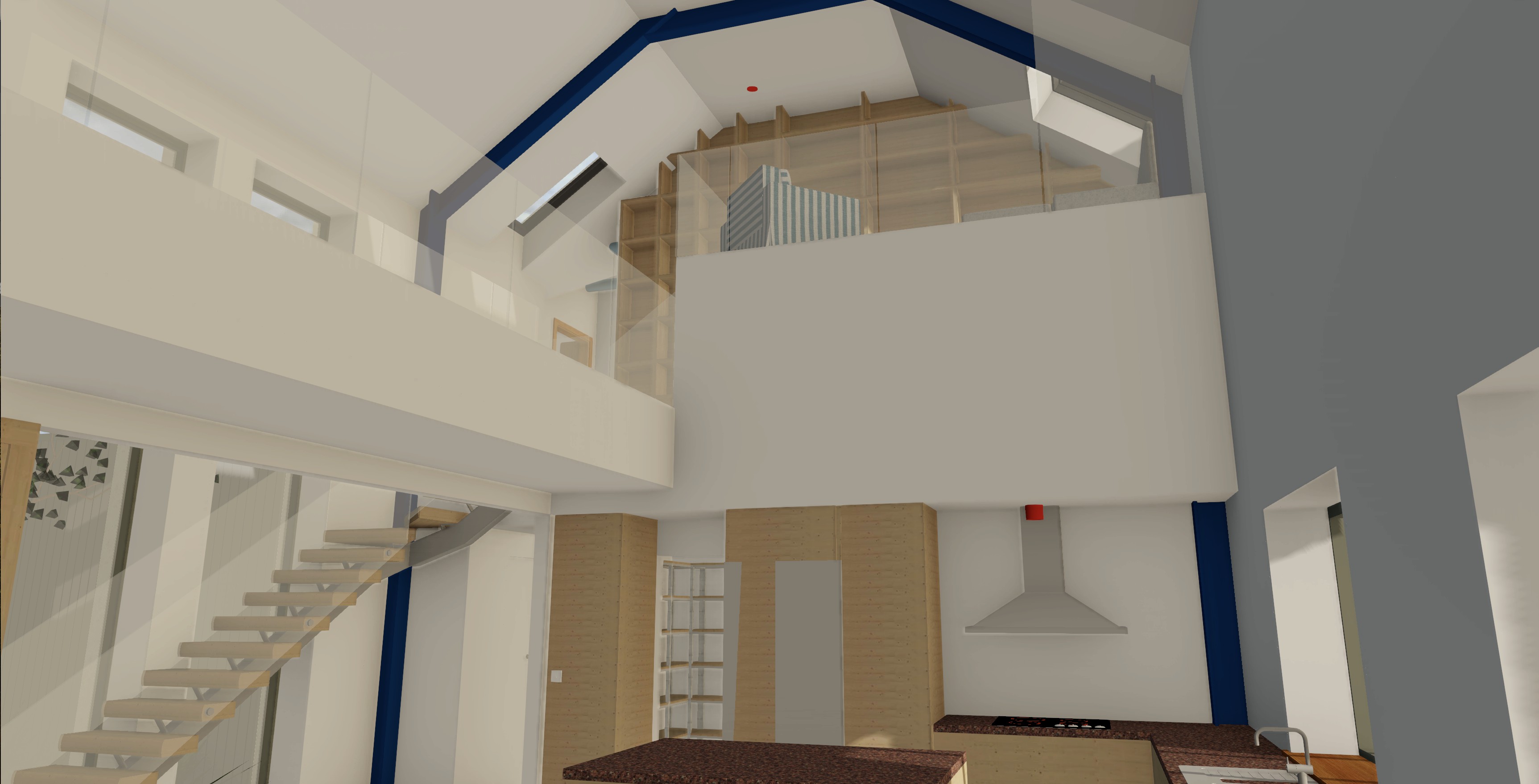
There is now a pronounced steel beam, coloured here blue (we will be using ochre red in reality). We deliberately have it exposed where possible now, so you can see it holding up the house over the mezzanine, and within the home office.
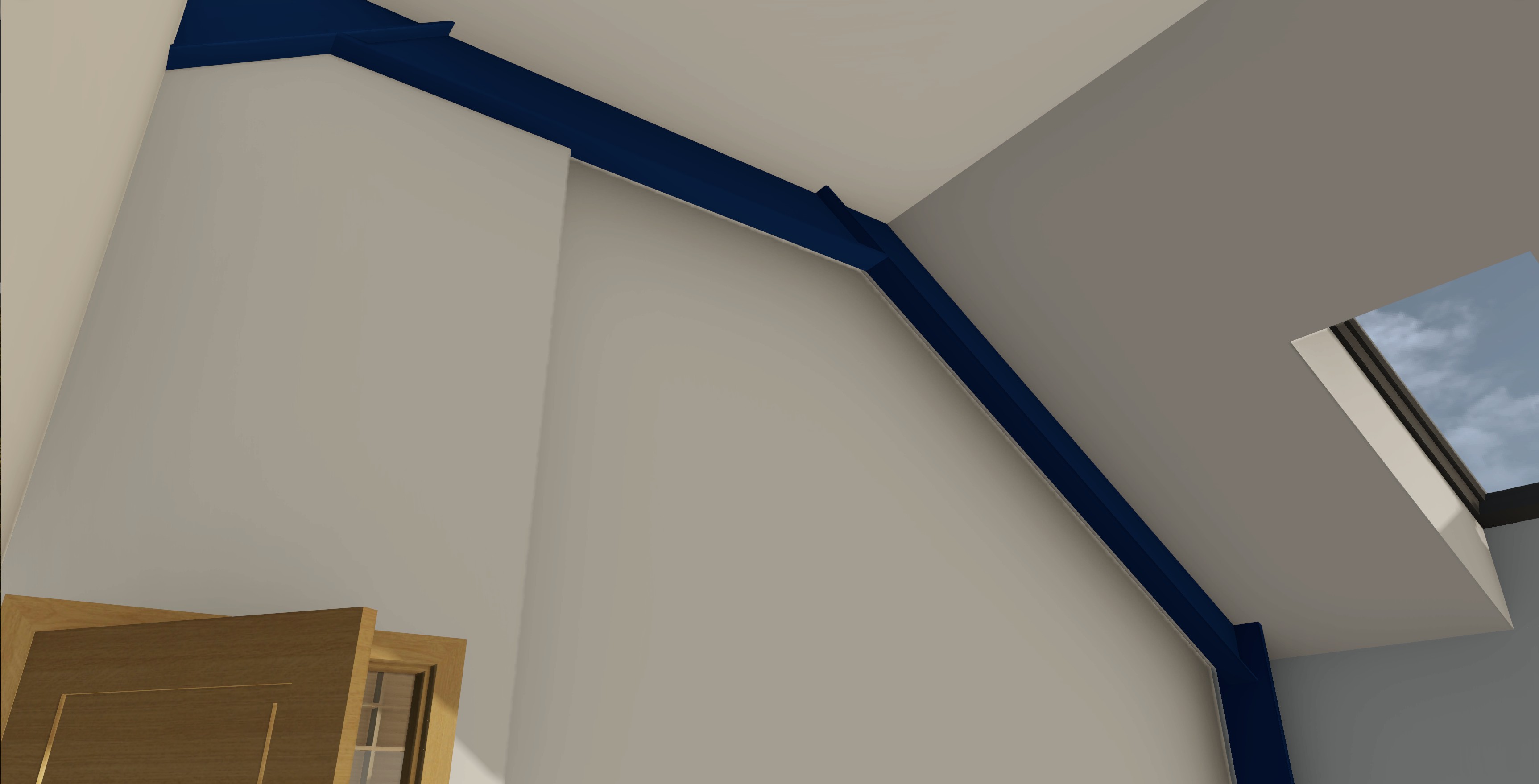
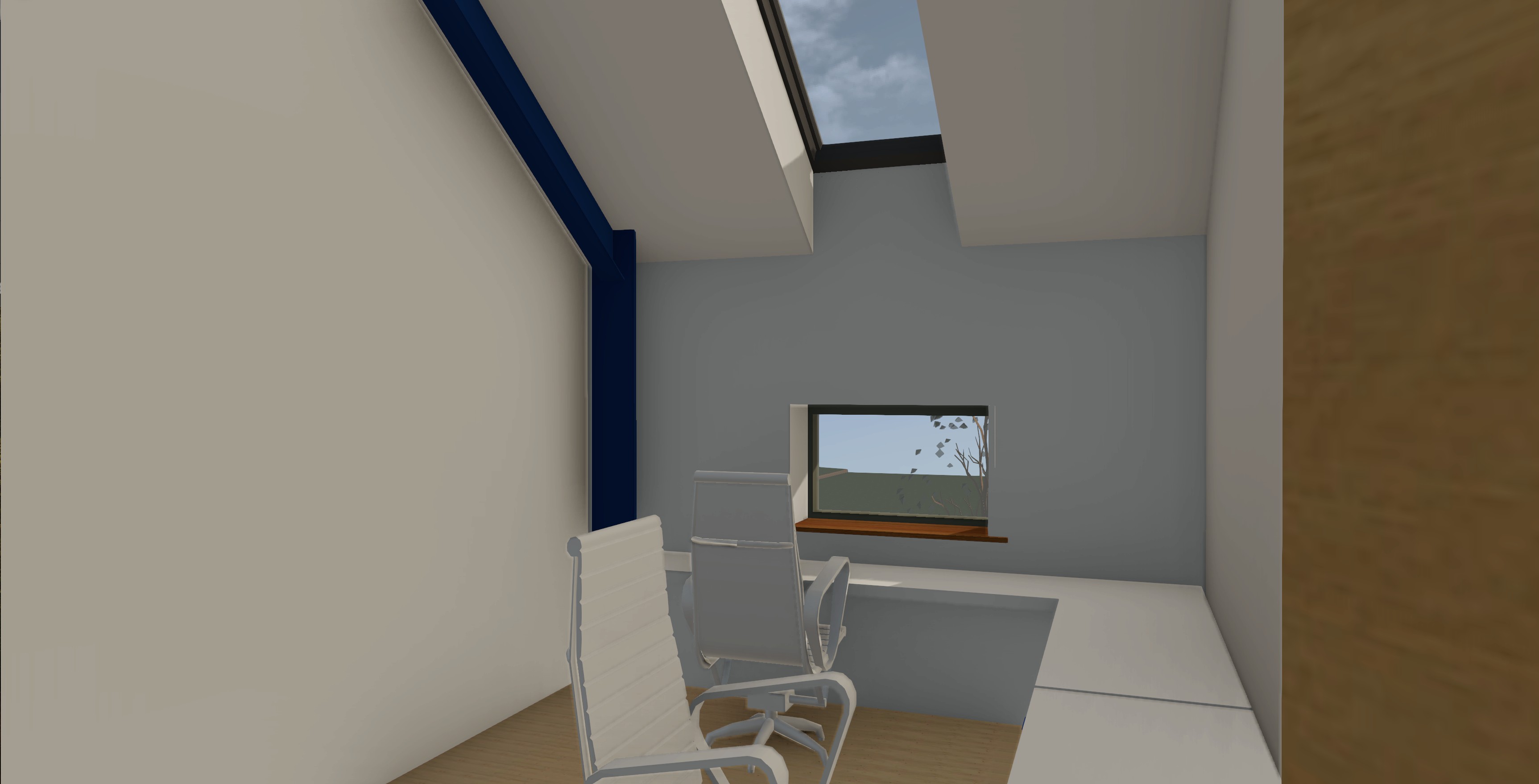
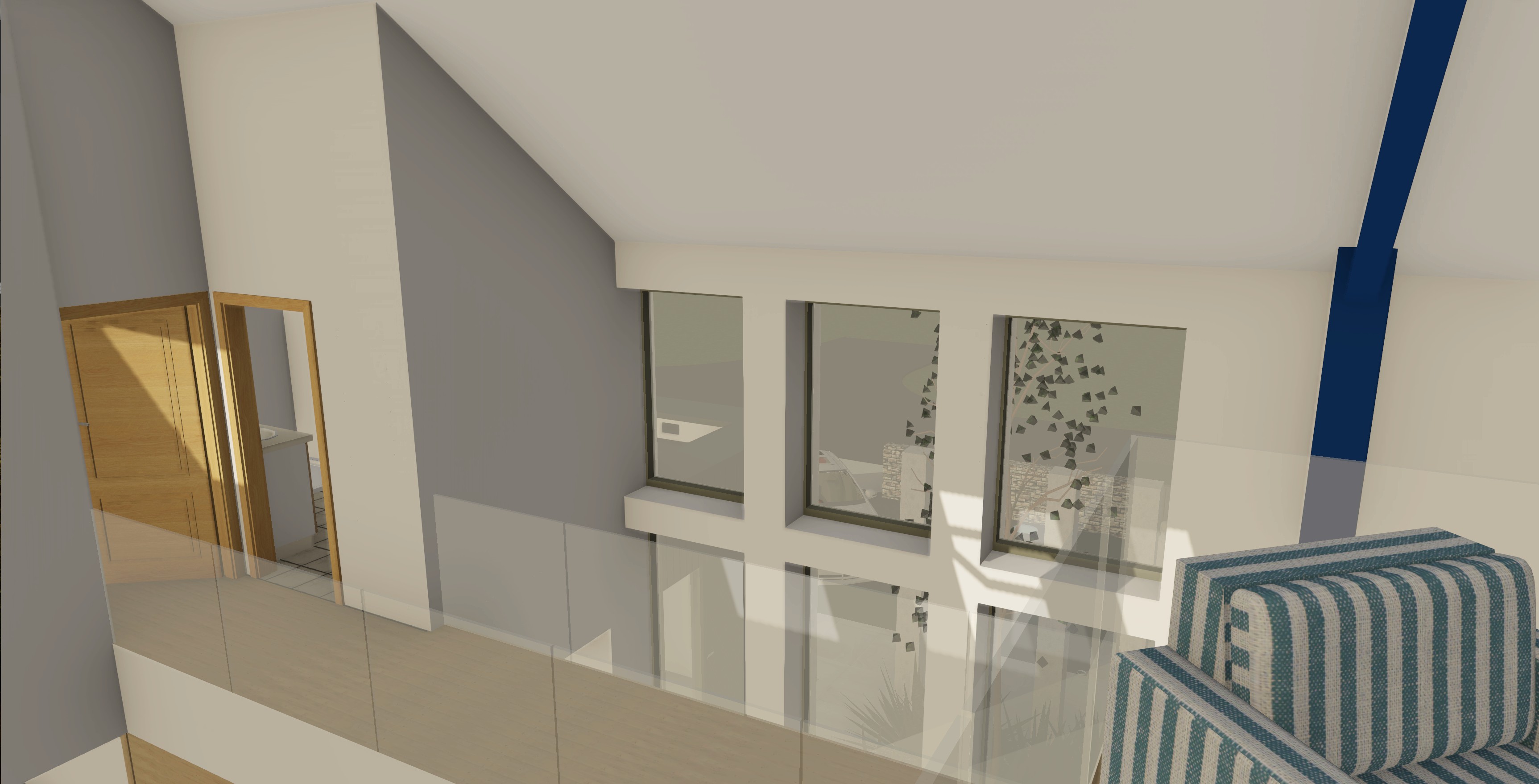
That last picture shows how the curtain glazing at the front has quite noticeably shrunk due to the walls going from 0.4m wide to 0.5m wide. Because both outer walls took 0.2m, but also the two columns in between, those windows went from over a metre wide to under a metre wide. They’re still the central feature of the house design, just not as pronounced as before. Obviously shrinking them did also have an outsize impact on heat loss to the north, so it greatly improved our PHPP numbers, and it’ll also reduce our glazing bill. Still, feels a bit of a shame, equally also very glad to be spending less on glazing now we’ll be spending more on structure.
Finally, there is an alternative render of the house which is kinda cool:
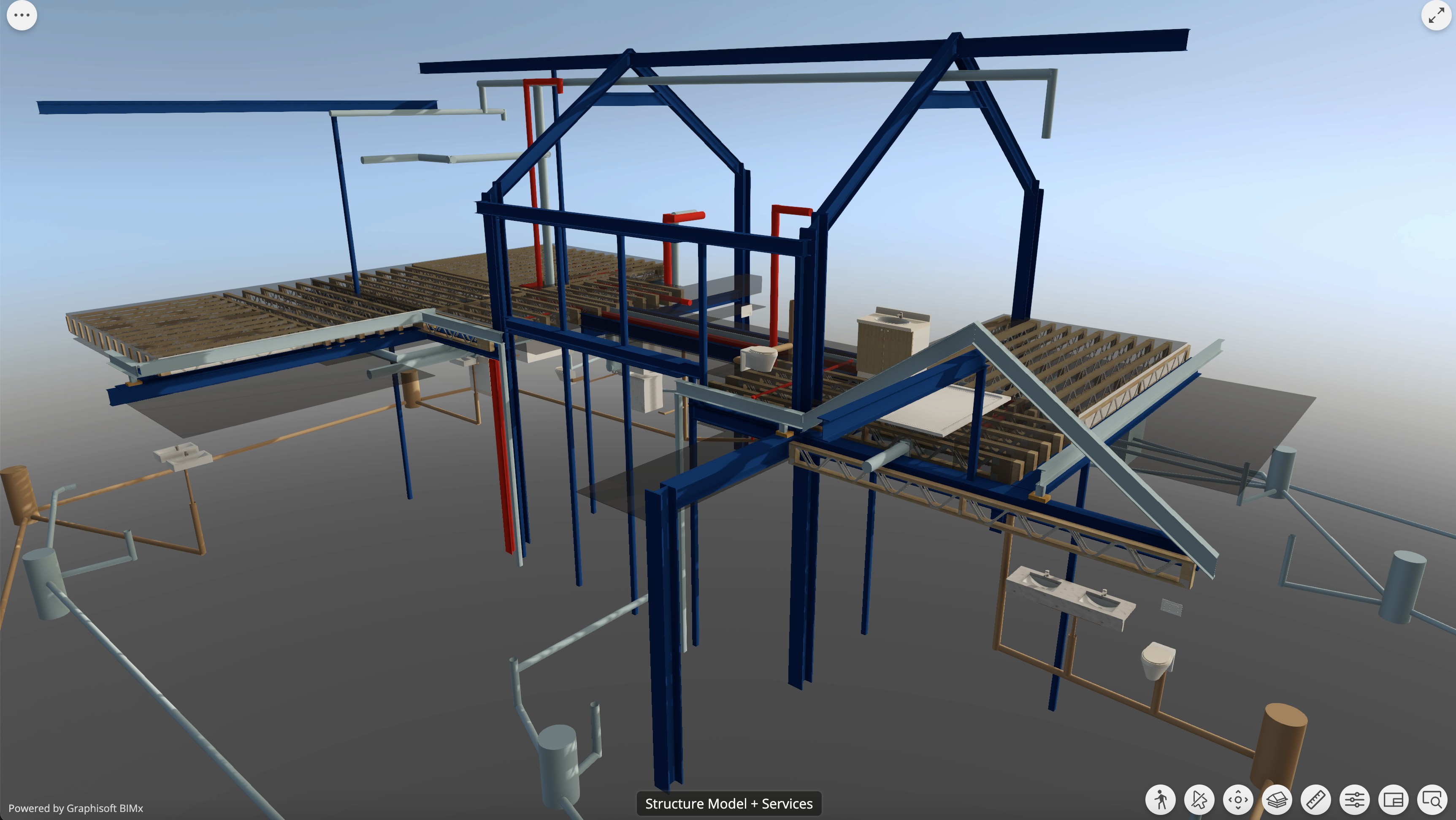
This is the house ‘nude’, as it were, so you can see all its drain pipes, ducts, joists and of course steel frames. Plus all of the gubbins which lives underground like sewerage and storm drains.
What’s next?
Now the €25k deposit is paid to LL Structures, the General Arrangement drawings will begin in about five weeks from from now, so last week of March. That might take a month, so to end of April. Then begins structural engineering design, which might take us to end of June. At this point off-site construction of the timber frames can begin, and the foundations and steel frame can be installed probably during July. The timber frame should therefore get erected in August.
Before then, we need to ‘commence’ before April in order to claim a development contribution levy subsidy. We think installing services popups and the base for the raft foundations is doable before then, so that’s the current next highest priority as it’s a saving of €13-15k or so.
Before we can do that, myself and Megan need to sign off on the final final final plans which once sent to the timber frame manufacturer shall be immutable forever! We’ll do that this weekend, unblocking everything else next week.
Go to previous entry | Go to next entry | Go back to the archive index | Go back to the latest entries |