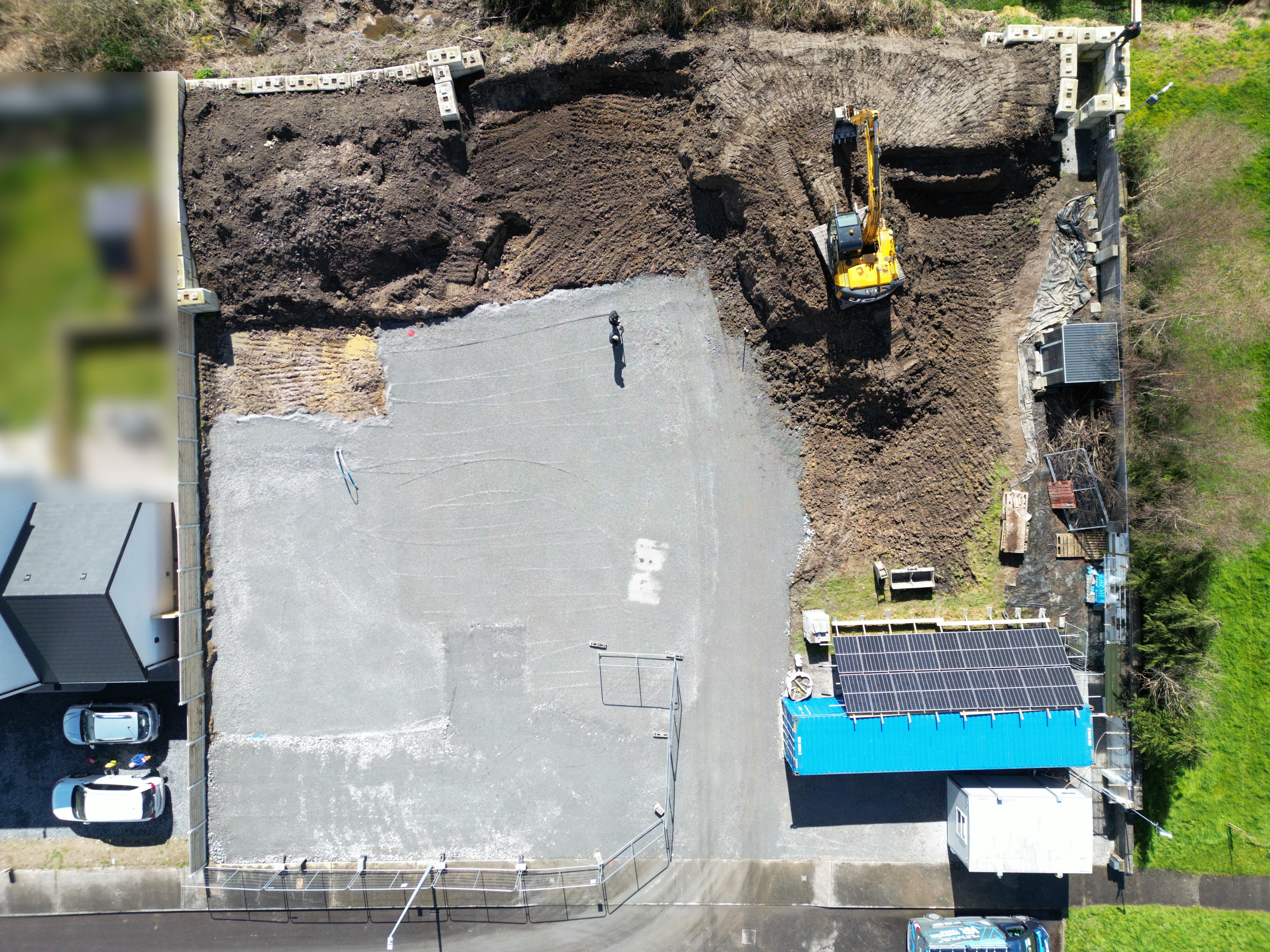
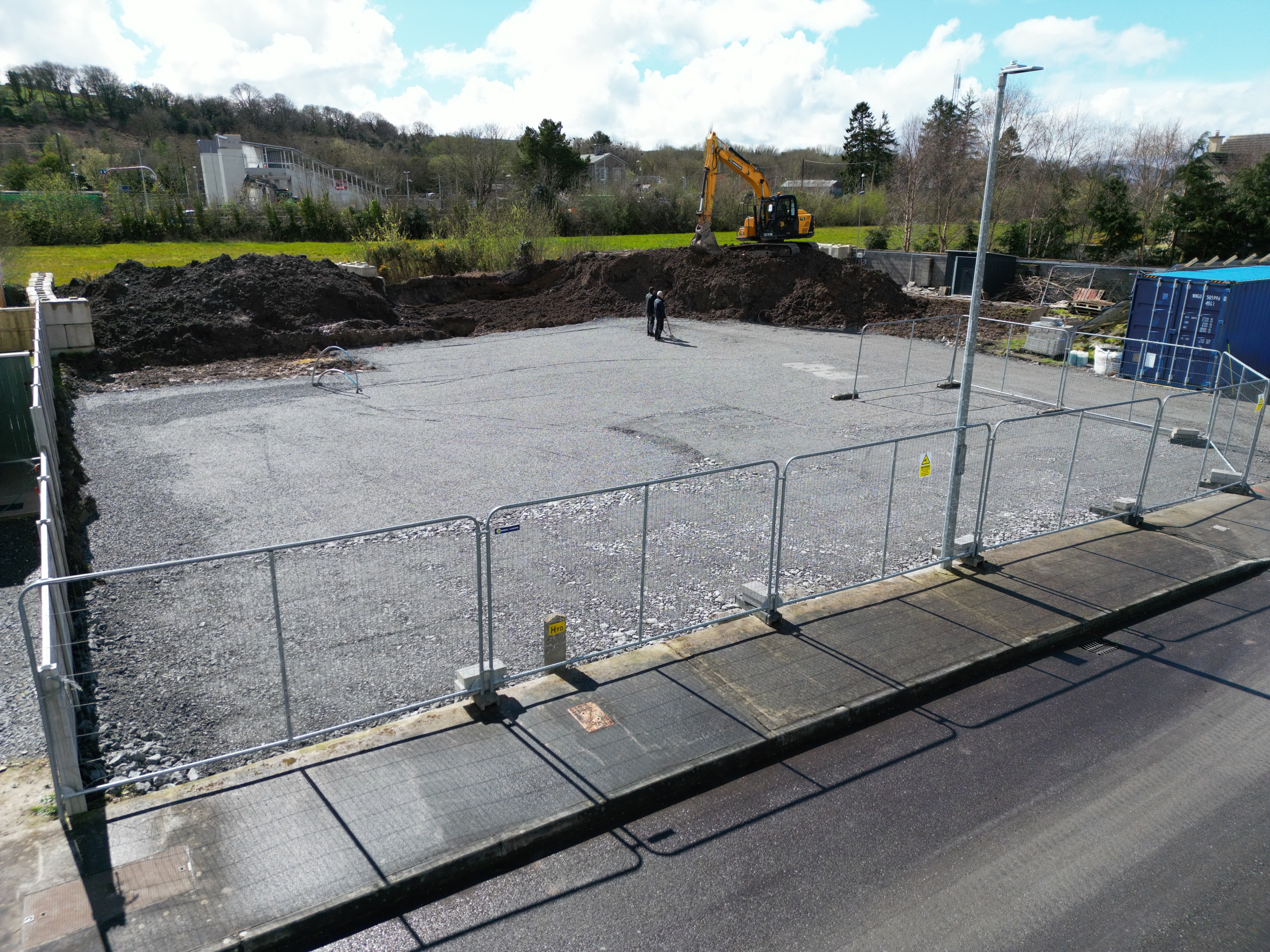
We ended up not fitting neither the land drain nor the soakaway as the soil 1.5 metres down turned out to be much more dry than expected, and thus capable of handling an inundation more than needing additional drainage:
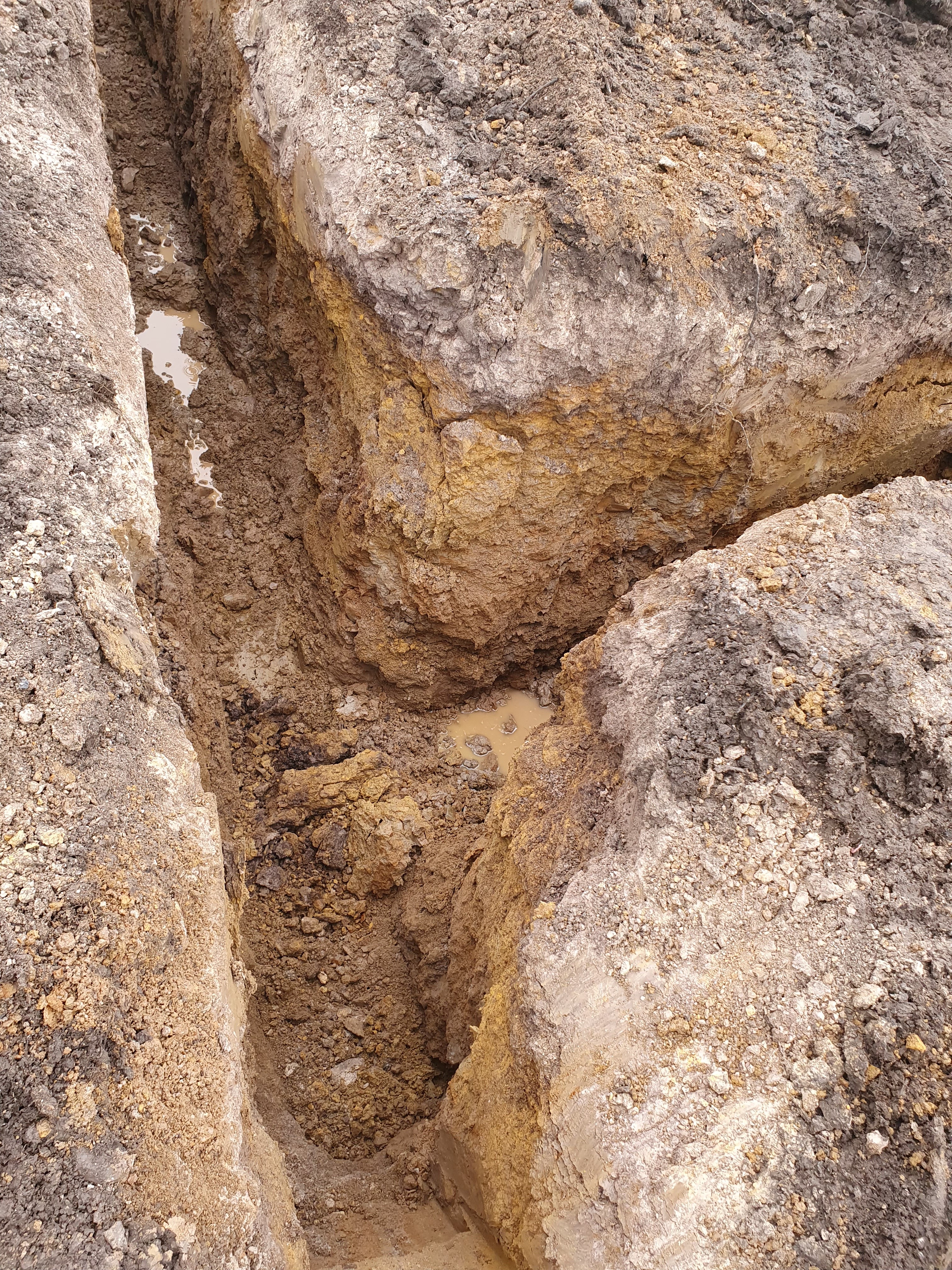
(the pool of water at the bottom shown is due to rain at the time, at the point of excavation the subsoil was surprisingly dry)
As the land drain would get crushed by heavy machinery if installed now, and seeing as it wasn’t necessary given how dry the subsoil is, we left it off until the outer block leaf gets erected, which is when the services will be installed.
First thing which went in is the subsoil heat exchanger, which is 150m of HDPE water pipe buried at 1.5 metres down. Here is its trench mid-completion:
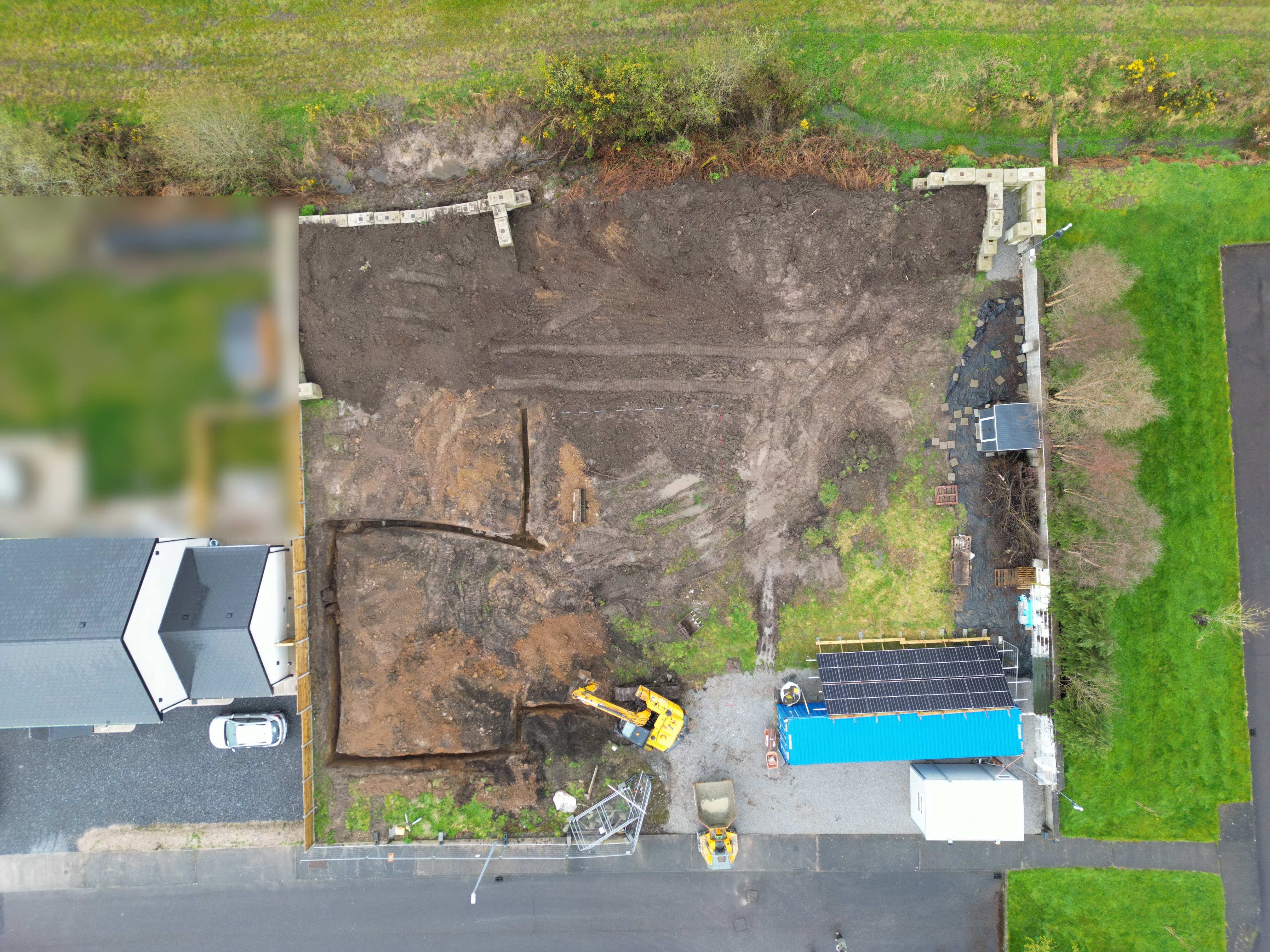
On top of that came a very great deal of T2 stone, which one of the truck drivers cheerfully informed me is one of the most expensive loads they do at €505 ex VAT per twenty tonne load. Yay. The stone came from the quarry at Ballyhest West, approx 13.2 km away from site. This is a quarry whose limestone originated in shallow waters and therefore has a distinctive blue tint, unlike the white limestone of deeper waters.
Last post I estimated that 150 m3 of T2 rock would be needed. I can tell you now that nineteen twenty metric tonne loads were delivered, which is 380 tonnes which is approx 190 m3. The reason we went a quarter over estimated is because some of the excavations exposed soft soil which had to be dug out deeper to reach subsoil. In particular, just under the master bedroom at the front right there was a €505 ex VAT costing hole, as that is what one truck load of T2 stone cost me:
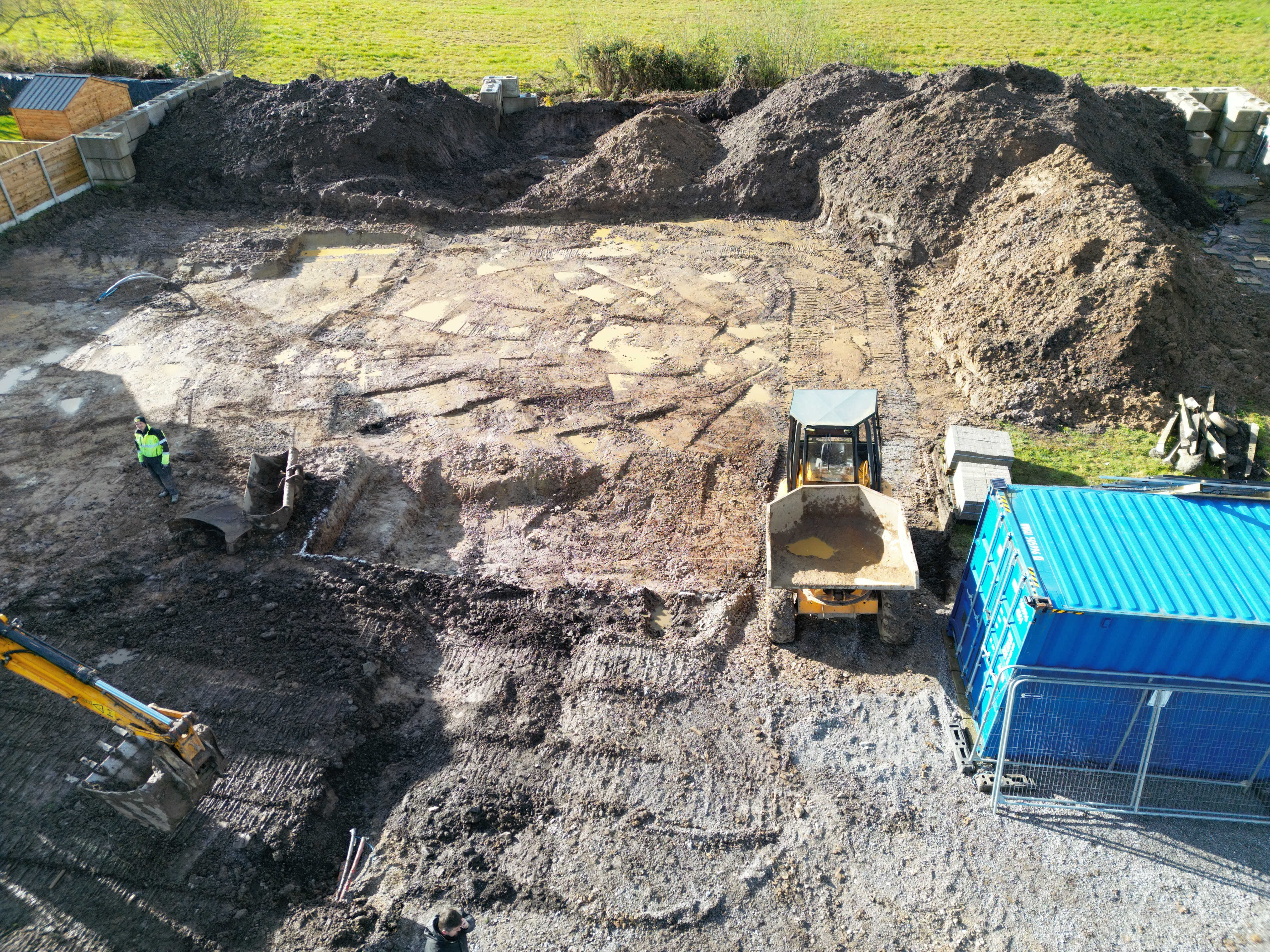
As much as I was rather wincing watching a full truck load fill what will be supporting my future bedroom and nothing more, it could have been far worse. One of my fellow neighbour self builders Patrick happened to pop by, and he was telling me how he had to drive forty-three piles to support the foundations of his future house. Due to driving piles, no insurer will cover his self build, and so he is exposed to unlimited liabilities if anything goes wrong. I spent two weeks trying to find somebody who would insure my self build. It turns out there are exactly three insurers on the current Irish market willing to underwrite a self build timber frame (there would be far more if it were a concrete block build aka ‘standard build’ (which is defined to exclusively be concrete block in Ireland), or if a main contractor were doing most of the work). Anyway I went with https://selfbuildprotect.ie which is a trading name for MDRB insurance, one of the larger brokers in Ireland for a cool €2,200 for eighteen months. If that seems a lot, it is, however it is proportional to the cost of rebuild which for me is rather a lot.
T2 stone is very much ‘expensive gravel’, it has the consistency of gravel, it looks like gravel, it feels like gravel, and it compacts like gravel i.e. it is barely worth running a whacker over it, though we did so anyway. Unfortunately it must be guaranteed cleaner than gravel, and you can see here the juxtaposition of the T2 stone with the cheap-as-possible gravel previously at the front of my site:
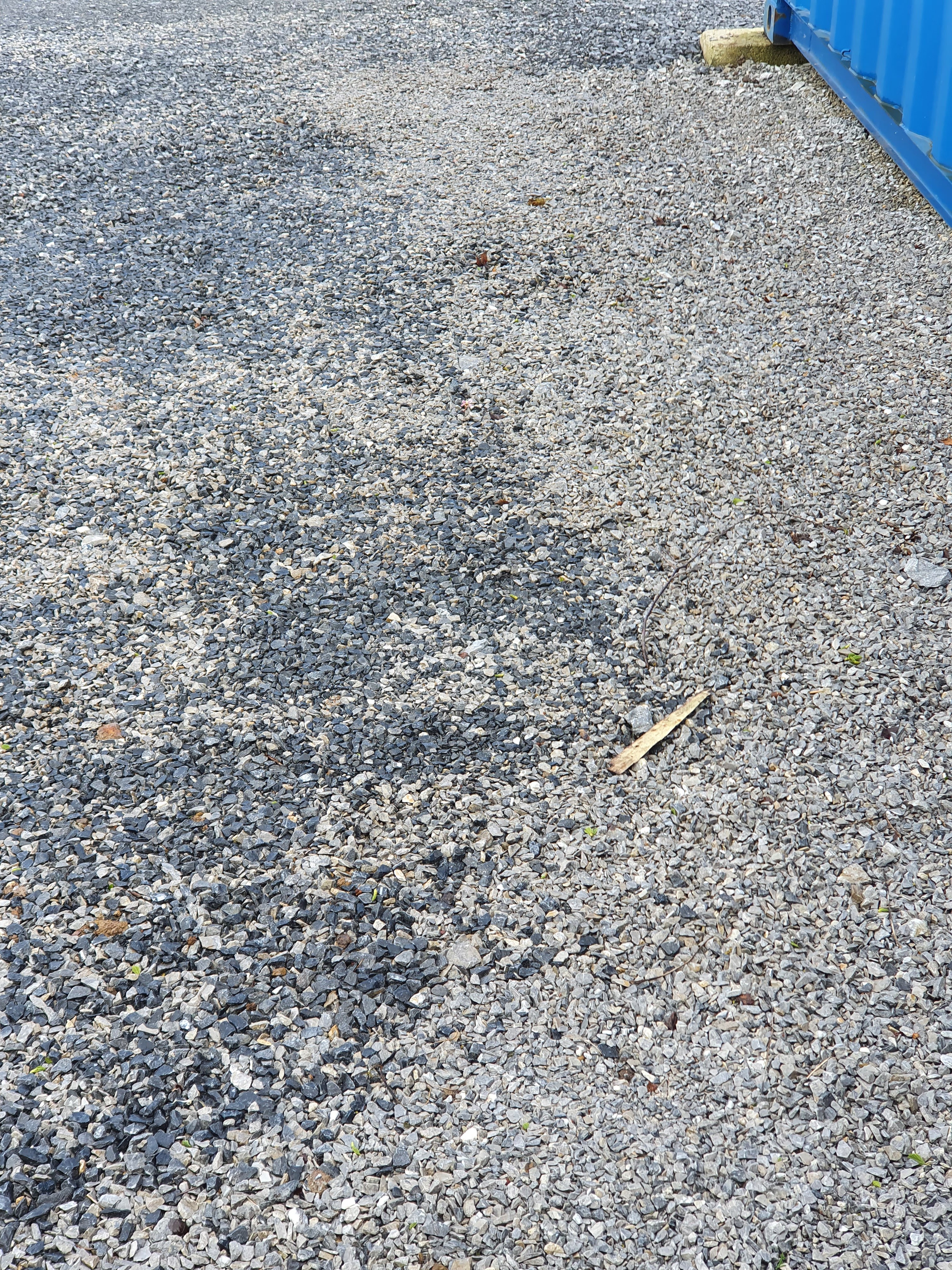
Both came from Ducon Concrete, whose head office is just up the road from me. But T2 stone comes with guarantees, whereas the cheapest possible chipped limestone from them does not. Hence the price (and colour) difference.
We did not in the end lay entirely T2 stone everywhere precisely because it really is like gravel i.e. unstable. We put four inch down towards the front where the future driveway will be, and then more four inch down to the right where the future patio will be, and between now and the future patio it will be where the heavy trucks will drive in. On top of the four inch down we put a layer of two inch down. Both four inch down and two inch down are quite a bit cheaper than T2 stone, so doing this saved me a few hundred euro. However unlike T2, both four inch and two inch down compact themselves into a rock solid surface almost like a road – indeed, this is what a Roman road was, compacted crushed rock of layers ever decreasing in granularity, and their roads lasted centuries before becoming unusable due to wear and tear.
Finally, a full twenty-three loads of soil were removed, at approx 20 tonnes per truck, which is four hundred and sixty tonnes of soil. So 380 tonnes of expensive stone in, 460 tonnes of soil out. Each truck of soil removal cost me €270 ex VAT, because I live in the EU and anything which could potentially involve waste removal is hideously expensive (in most parts of the world topsoil removal means them paying you for the topsoil, but not in the EU where removing a valuable commodity costs you money). In case you’re wondering why?, the answer is apparently any unregulated transfer of soil from anywhere to anywhere else comes with a €50,000 fine. So basically due to regulatory capture, the price of disposing of anything at all gets tainted by the 1% of disposals which are very expensive to dispose of, and for obvious reasons if you’re disposing of toxic waste you’re getting an absolutely wonderful deal at €270 ex VAT per tonne with the costs spread onto everybody else. Yay.
What may not be obvious from the photos is we kept the very best of the topsoil which is a dark brown material, very very good topsoil. That is currently a three metre high mound in our future walled garden.
As much as installing the pre-foundations cost me at least €20k (I haven’t actually gotten the bill yet, but at least that much materials went in or were removed), it does leave a rather pleasant ‘sea of stone’ which even walking around is somewhat satisfying. Here it is being flown around by the drone:
In case you were wondering, the stoned levelled area is approx 630 m2. The total site is 1400 m2. So, approximately 45% of the total site will be put under stone initially, with pockets later carved out as grass. I very much agree that it doesn’t look like half the site by area has been stoned – it looks like much more – but that there is what the maths says.
Outhouse
The groundworks guys double-triple-quadruple recommended to me in the strongest possible terms to not lay the sewers for the house until no more heavy machinery would be traversing the site. That effectively means that us moving into our house is blocked by the completion of the outhouse, so it has just leapt up the priority queue.
To be honest, I really hadn’t given it much thought until now outside its basic design which was needed for planning permission, which is this:
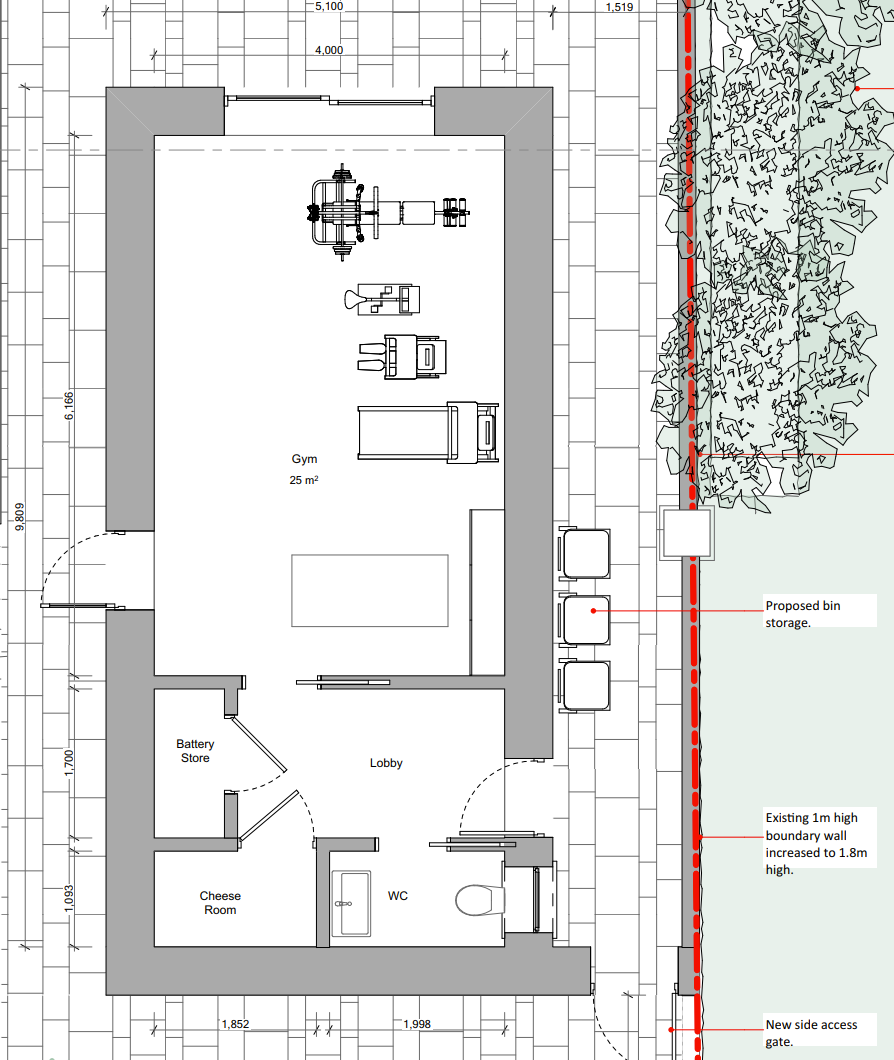
Neither me, my architect, nor anybody else has touched that design in well over a year. It’s been that low priority.
I had had some ideas of maybe building it with ICF i.e. polystyrene hollow blocks you pour concrete down the insides of. But the house quotes I got for ICF were ridiculous, and for a crew to come out to do a small box 10.36 x 5.1 metres there would surely be a substantial premium for them turning up at all.
I could do timber frame again for the outhouse … but that kinda feels lazy. Plus, I really don’t need passive spec for the outhouse, and as it’ll mainly be a gym, concrete block inside walls would be very attractive for hanging mirrors, bars and other heavy things. Plus, painted concrete blocks is very much how gyms are, so it would give the desired ‘feel’.
That got me onto wondering how you’d do this if it were a conventional new build in Ireland, how much that would cost and so on. Generally new builds in Ireland are still strip foundations where you dig out where the walls will be to about 1.2 metres down, fill the bottom of that trench will liquid concrete to provide a footing, then raise the walls using block on flat from there (often called the deadwork, as it’s all underground). As you near the floor level, you switch to expensive aerated concrete blocks to provide a thermal break, usually three layers, with 200 mm of expanded polystyrene (EPS) insulation under the room floors and a 50 mm screed to yield a floor with an average 0.18 u-value, which is the legal maximum in Ireland since 2019.
Note my qualifier ‘average’. Those aerated concrete blocks they have seven times lower thermal conductivity than standard concrete blocks, but EPS has a thermal conductivity 42.9 times better. If you are perforating your floor insulation at regular intervals with a thermal bridge seven times more thermally conductive, you get much worse quality floor insulation. Yes, the average might be good, but it won’t be even, there will be ‘cold spots’ and if they are cold enough relative to moist air, they’ll condense i.e. you get mould. Most new Irish builds even post 2019 regs still develop mould after a few years – much better than pre-2019 no doubt where some of those new builds became riddled with mould within a year. But still, not great.
It would annoy me if my gym got mould into it, so I’m rather liking the idea of wrapping the foundations in continuous EPS so there are zero thermal breaks. In fact, let’s just wrap the whole building in unbroken EPS:
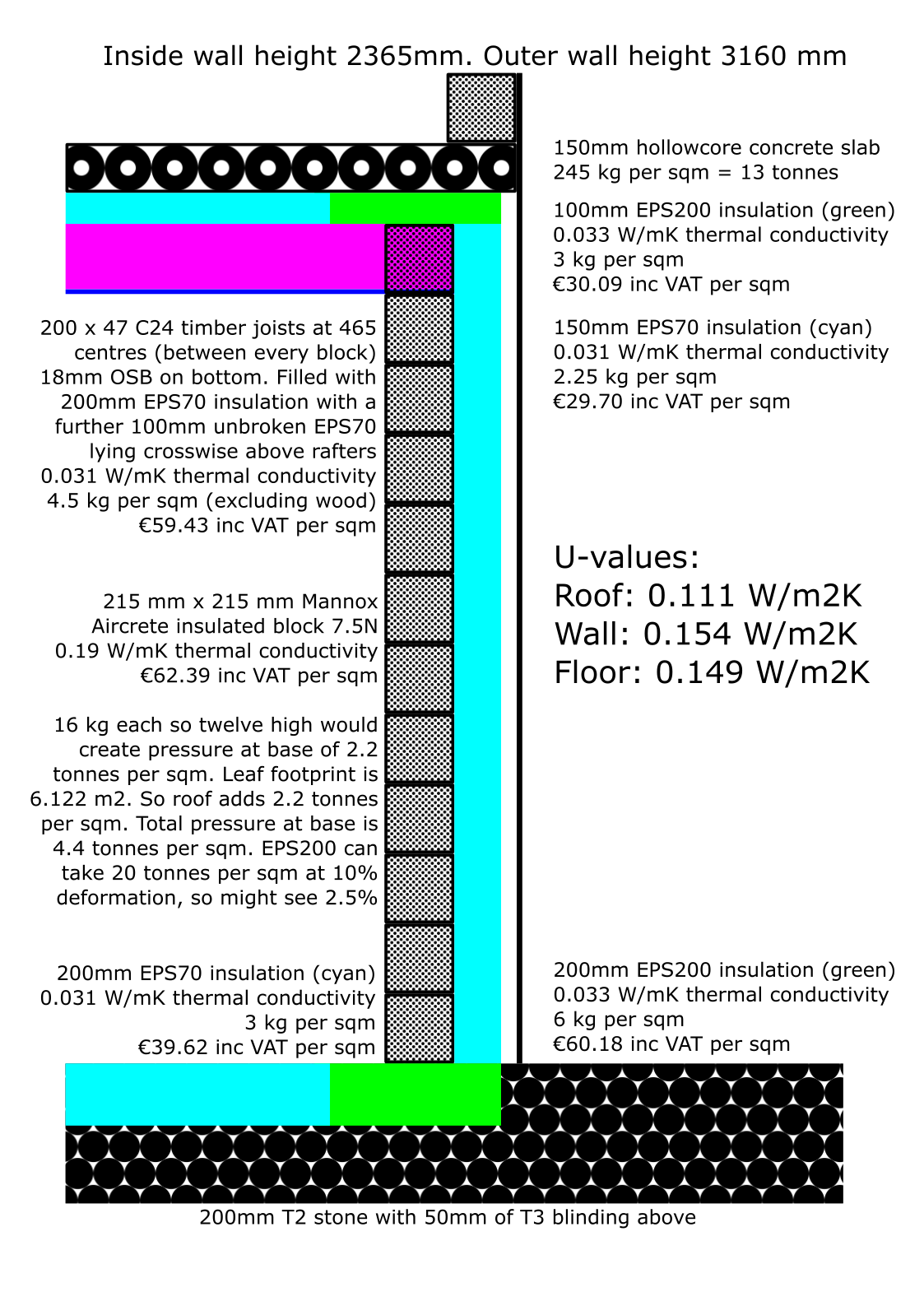
All the above is 100% my design and calculations, and I am neither an architect nor the right kind of engineer. Still, designing the main house has gotten me much more familiar with structural and thermal design than I was. A simple box of a building is now well within my capabilities, and I kinda enjoyed testing my new skillset above.
You might wonder why use the expensive aerated blocks within when they are completely thermally broken from the outside? It’s a good point, and that may get jettisoned yet for cost reasons as they are more expensive per sqm than anything else. Standard concrete blocks cost about €30 inc VAT per sqm, so less than half the cost. I had been thinking weight reduction, but also that you wouldn’t get problems such as condensation on these from sudden temperature changes which will be likely, as the gym won’t be in continuous use and will instead usually go from cold to warm very quickly for short periods of use.
The other thing I’d like to get rid of is the concrete slab for the roof if possible. It creates a cold roof and all the insulation being on the inside will risk interstitial condensation. It would be better if the insulation went right up to the flat roof membrane, thus making a warm roof. However to achieve that, I can’t see any way of avoiding the roof joists themselves becoming thermal bridges as they’d need to poke out far enough to provide shelter for the wall insulation. At 0.13 W/mK timber is better than those aerated concrete blocks, but still many many times worse than EPS. I would also need a continuous slab of EPS200 between the joists and the roof membrane, which is €1,600 inc VAT of EPS just for that alone.
Or would I? What actual weight lies on that roof? EPS70 can take seven metric tonnes per sqm with a deformation of under ten percent, and there is absolutely zero chance of that kind of weight.
The KORE EPS70 comes in 600 x 1200 slabs, so I’m wondering if I made the roof joists at 600 centres, a 220 x 44 joist should span 4.385 metres and the gap between the inside walls is 4.27 metres. The other package for KORE EPS70 comes in 1200 x 1800 slabs (exact same price per sqm), so if a warm roof won’t take much load, why not sandwich a 80 mm EPS70 board between two 18mm OSB sheets, and that’s your warm flat roof?
I reckon such a build up would have a roof u-value of 0.12 W/m2K; if the EPS70 between the OSB boards were 50 mm instead, then 0.135 W/m2K. That does feel more cost effective, and maybe I’ll do up the detail for that with costings at a later point.
Anyway, for the detail above:
- There is 52.84 m2 of roof and floor, let’s call that 53.
- There is 89.67 m2 of wall minus approx 13 m2 of glazing = 77 m2.
- 13 m3 of T2/T3 stone needed which would be 26 tonnes or so, so €600 inc VAT.
- Twenty-two lengths of 220 x 44 x 6m wood needed at €35 inc VAT each is €770 inc VAT total.
- Approx €3,150 inc VAT for the roof insulation.
- Approx €2,100 inc VAT for the floor insulation.
- Approx €2,300 inc VAT for the wall insulation.
- Approx €4,804 inc VAT for the insulated block wall.
- Approx €6k inc VAT for the charred larch outer cladding.
- Approx €8k inc VAT for the glazing.
- Approx €28k inc VAT in total excluding labour.
Obviously I omitted the hollowcore slab as I’m hoping to engineer it out of being needed, but it seems reasonable to me I can get that outhouse done for about €50k inc VAT or thereabouts. I originally had €80k inc VAT as a guessestimate, so that’s rather better than expected back when I first started planning this a very long time ago.
Anyway bed time for me! I should send some emails enquiring about progress before I go to bed …
Go to previous entry | Go to next entry | Go back to the archive index | Go back to the latest entries |